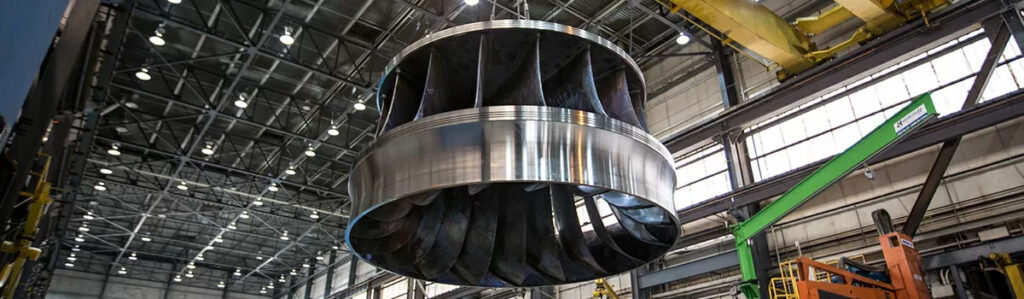
A representative hydro turbine from GE Renewable Energy (© GE Renewable Energy; photo: Business Wire)
The new manufacturing technology will produce metallic, near net-shape (NNS) components that reduce production time and costs for the wind and hydro energy sectors.
FRIEDBERG, Germany—GE Research recently selected Voxeljet (stylized as voxeljet) as its partner for a U.S. Department of Energy (DoE) contract award to develop novel manufacturing technologies. The $14.9 million DoE grant will fund the development and commercialization of a large 3D sand printer to help enable the transition to clean power in the United States, according to a release from voxeljet.
The sand binder jet 3D printer, or Advanced Casting Cell (ACC), will be used to manufacture massive sand molds for casting parts ranging in weight from 10 tons to 60 tons. In addition to voxeljet, GE Research has also selected GE Hydro, GE Onshore Wind, GE Offshore Wind, Clemson University, Oak Ridge National Laboratory (ORNL), and Hodge Foundry as partners on the ACC project, voxeljet said in the release.
The Advanced Casting Cell project was established to strengthen the U.S. manufacturing industry by boosting the cost-effective domestic production of large, metallic, near net-shape (NNS) components, in alignment with the Biden Administration’s clean power-generation strategy. The ACC will be developed and deployed to produce sand molds to manufacture metallic NNS parts. With development of the ACC, the project includes the digital creation of mold designs via a digital foundry, as well as the completion of a techno-economic analysis of cost and supply chain challenges, the company said.
The project aims to produce 3D-printed, large scale sand molds to cast components for the nacelle of the GE Haliade-X Offshore Turbine. The nacelle, where mechanical components are housed, can weigh more than 60 metric tons. The goal is to reduce the time it takes to produce this pattern and mold, from about 10 weeks to two weeks. According to Data Bridge Market Research, the global wind turbine nacelle market was estimated to be valued at $6.6 billion in 2021. It is projected to exceed $15 billion by 2029, the release said.
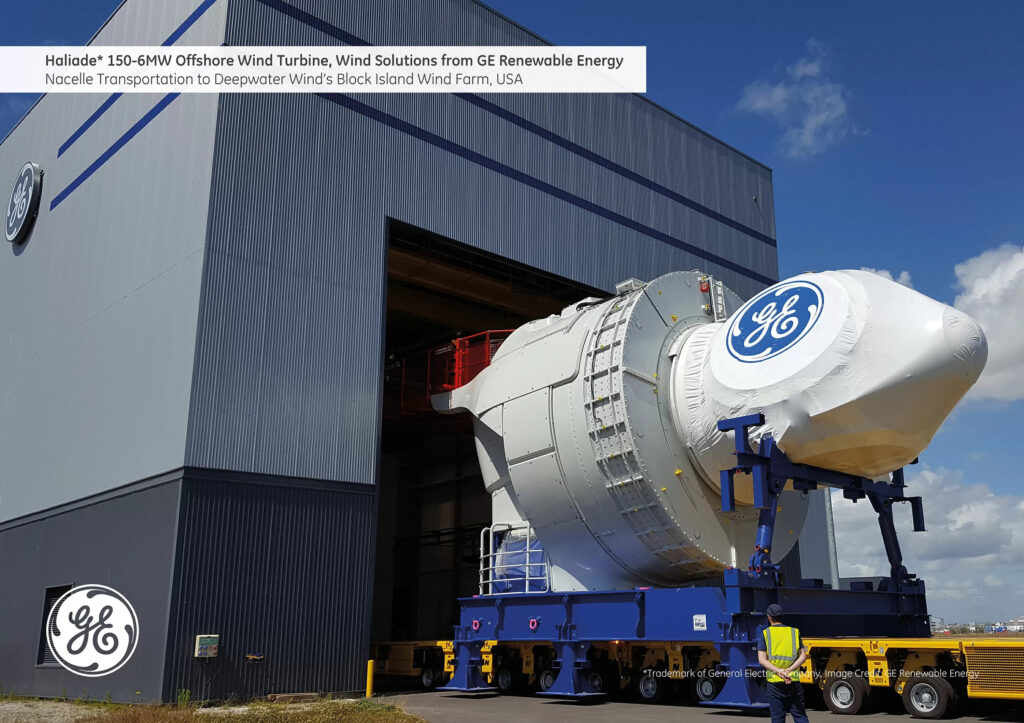
An offshore wind turbine from GE Renewable Energy. (© GE Renewable Energy; photo: Business Wire)
According to voxeljet, this novel manufacturing technology has the potential to reduce overall hydropower costs by 20 percent, and lead times by four months. The project will include the production optimization of a 16-ton rotor hub using the ACC, as well as the development of a robotic welding process for the assembly of a Francis runner weighing more than 10 tons. To help develop a local workforce and ensure successful implementation of ACC, an advanced manufacturing curriculum will be created to train and engage workers on the specifics of this 3D printing manufacturing technology.
“We’re excited to be a part of this future-driven and innovative project,” said voxeljet CEO Ingo Ederer, in a statement. “The development and cost-efficient manufacturing of clean power-generation technologies is in high demand because it is key to meeting and overcoming global climate challenges. We are confident that additive manufacturing, and specifically, our large-scale Binder Jetting technology, is the right choice to manufacture complex parts used in these next-generation wind turbines.”