This sets a new milestone in their expansive portfolio of professional and industrial 3D printing solutions, marking their debut in photopolymer resin 3D printing.
Rotterdam, 7th November 2023 – Raise3D, the flexible manufacturing solutions provider, is proudly unveiling the DF2 Solution today at Formnext. It’s a new milestone in their expansive portfolio of professional and industrial 3D printing, marking their debut in photopolymer resin 3D printing. The DF2 Solution, based on Digital Light Printing (DLP) technology, boasts rapid printing speeds, refined surfaces, high precision, and remarkable reliability. It has been meticulously crafted for engineering prototyping, manufacturing aids, and low-volume production with a diverse selection of high-grade resins. The DF2 Solution features a traceable workflow to reduce labor time and optimize the use of resin 3D printing in production.
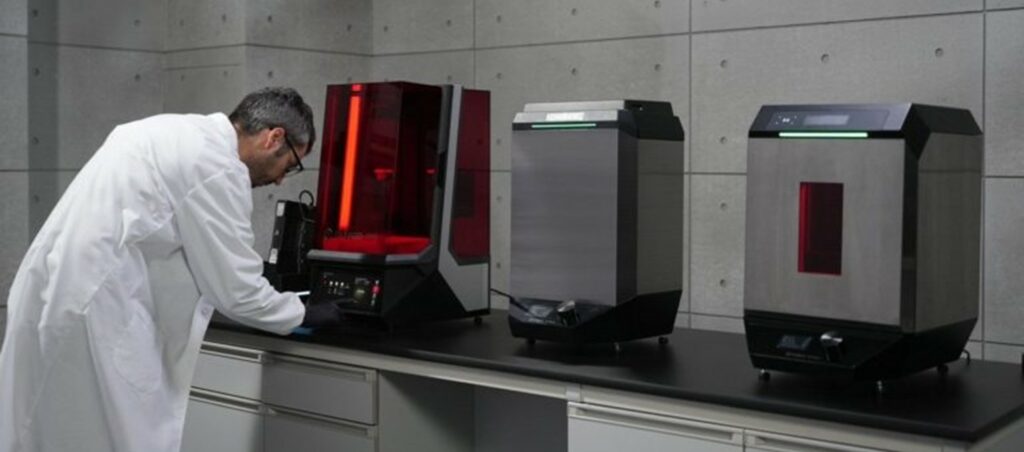
Figure 1: The Raise3D DF2 Solution
The DF2 Solution offered by Raise3D integrates several components to deliver a complete 3D printing workflow:
- Raise3D DF2 3D Printer: A DLP printer for producing low-volume high-resolution, smooth and repeatable parts, thanks to its precise and reliable Z-Axis lifting system, efficient material management, heated chamber, high quality optical system, advanced Anti-Aliasing technology and Air-Peel technology for fast and easy layer detachment.
- Raise3D DF Wash: An automated cleaning solution with efficient process control, and ease of maintenance. It boasts robust cleaning capabilities via twin-turbine washing and hand washing simulation, and a double-fan air drying system. It accommodates various cleaning agents like alcohol, IPA, TPM, and water.
- Raise3D DF Cure: An advanced curing station equipped with multiple UV curing and heating profiles. It utilizes dual curing sources across multiple wavelengths (365/385/405 nm).
- ideaMaker Slicing Software: Adapted for the DF2 Solution, this software simplifies the DLP printing process. Features offered include antialiasing, auto support, contour compensation, suction cup detection, texture generation, and a reduced Gcode size, among others.
Resin Material Strategy
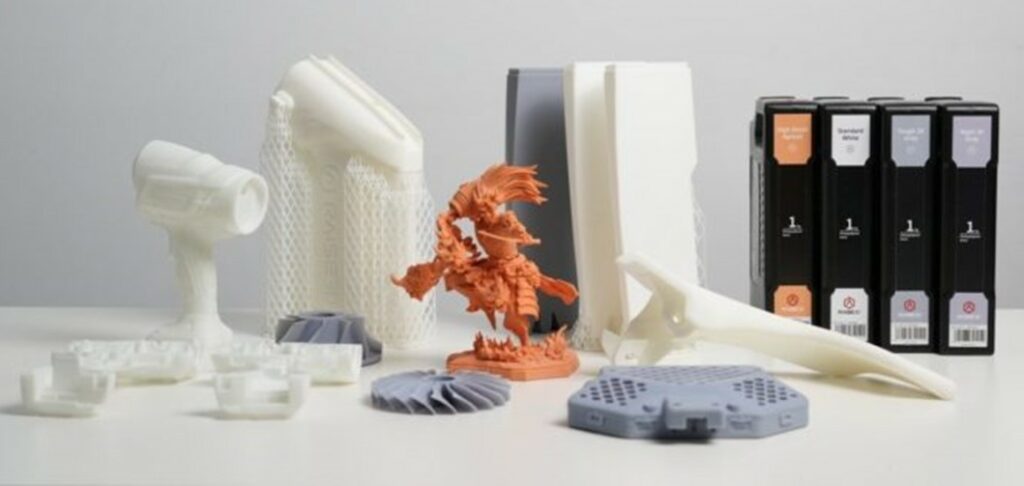
Figure 2: Raise3D Resins
Raise3D continues its commitment to innovation with ongoing investment in resin development. A wide variety of materials are on the horizon, such as high temperature resin, for production-grade end-use parts that meet special application needs and that drive technological advancement.
The company recognizes the integral role that resin material development plays in advancing 3D printing applications. For this reason, Raise3D is proud to add resin development as a core competency within their organization, with an ongoing reallocation of internal resources to advance it.
As part of the company strategy, the Raise3D DF2 Solution will continue to support an open material platform for innovation to empower their customers to explore new possibilities in resin 3D printing. With the launch of the DF2 Solution, Raise3D is pleased to announce the ORP (Open Resin Program). A collaboration between Raise3D and Resin Manufacturers to identify and select top-performing resins for the Raise3D DF2 Solution.
Traceable and Easy Operations
- Smart Build Plate Technology: The smart build plate seamlessly integrates with post-processing devices, thanks to embedded RFID tags that record the type of resin being used, in addition to washing and curing settings. This allows operators to manage the washing and curing phases with ease, regardless of their familiarity with the products being produced.
- Streamlined Resin Management: Boasts features such as Auto Resin Refill, Resin Material Auto-Recognition, Ultrasonic Liquid Level Monitoring, and Assisted Resin Tank Cleanup.
- Faster and better prints: Raise3D’s Air-Peel technology significantly decreases peeling force, making layer removal from the film faster during printing. This innovation is supported by an ultra-thin air film that facilitates smoother peeling and enhances printing speed and isotropic properties of printed products.
Superior Print Quality
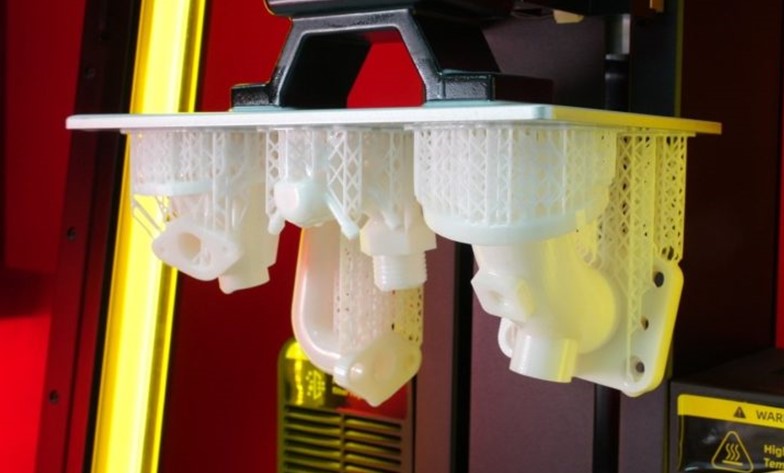
Figure 3: 3rd generation smart lattice support
- Optimal Optical Components: These minimize loss and eliminate dispersion, ensuring the reproduction of sharp layers, for best durability and image quality.
- Precise and smooth surfaces: Boasting a 78.5 μm XY Pixel and 2560 x 1440 resolution, the DF2 can achieve detailed and smooth prints every time, as a result of not just superior hardware but also the integration of sophisticated Anti-Aliasing technology.
- Optimized Print Success: The 3rd generation smart lattice support ensures a high rate of print success, reducing the likelihood of operator’s errors. The advanced support structure is also designed to minimize residual marks, lessening the need for post-print sanding or finishing.
Enhanced Reliability
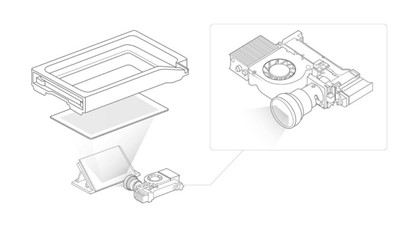
Figure 4: Raise3D DF2 Solution state-of-the-art light engine
- State-of-the-Art Light Engine: The DF2 Solution is built with high-quality components for long-lasting use and excellent image clarity. The core light engine features curated LED light sources, a DMD chip dedicated for 405 nm 3D Printing, and a low-distortion glass lens optimized for DLP technology.
- Precise Optical Control: The DF2 resin printer leverages advanced machine vision technology for system calibration, ensuring accuracy at every step. Additionally, each unit arrives pre-calibrated from the factory, ready for immediate operation.
- Stable Printing Environment: The DF2’s heated chamber ensures stable temperatures essential for consistent printing outcomes, particularly when using specialty resins that demand a heated environment. The printer’s dust and spill-proof design further guarantees sustained performance and durability.
Efficient and Safe Workflow

Figure 5: Raise3D DF Wash how it works
- Reduced Manual Tasks: Automated drainage with an easy-to-operate automatic pump and door mechanisms that minimize the need for manual intervention.
- Effortless Maintenance: The DF Wash flushing system streamlines the solvent removal process from the wash station, enhancing cleaning efficiency while minimizing user contact with chemical residues.
- Versatile: The DF Cure’s spacious curing area accommodates large models, and multi-wavelength curing ensures compatibility with various resins.
Q&A
Why did Raise3D develop the DF2 Solution? The DF2 Solution was designed to expand Raise3D’s FFF technology, addressing the varied needs of users in different application scenarios. With a focus on engineering applications, it provides high precision and smooth surfaces, reliable performance, and a streamlined printing process. Furthermore, Raise3D identified several production applications where the combined use of FFF and DLP 3D printing is ideal. The DF2 Solution enables users to conduct prototype verification across several application fields and facilitates small-batch production of intricately detailed and consistent components.
Edward Feng, Raise3D CEO says, “Our goal has always been to make resin printing hassle-free for production, with unmatched repeatability, unparalleled quality, and remarkable speed. With the DF2 Solution, we are proud to have achieved a solid step in this direction.”
Why the choice of DLP Technology? Raise3D’s adoption of DLP technology stems from its commitment in providing the finest balance of accuracy, speed, stability, and light source stability and longevity to its clientele. After careful evaluations, the company established DLP technology as the most suitable for production scenarios. The DLP projectors maintain consistent pixel count regardless of print size, offering numerous advantages over LCD and SLA technologies as described in the image below.