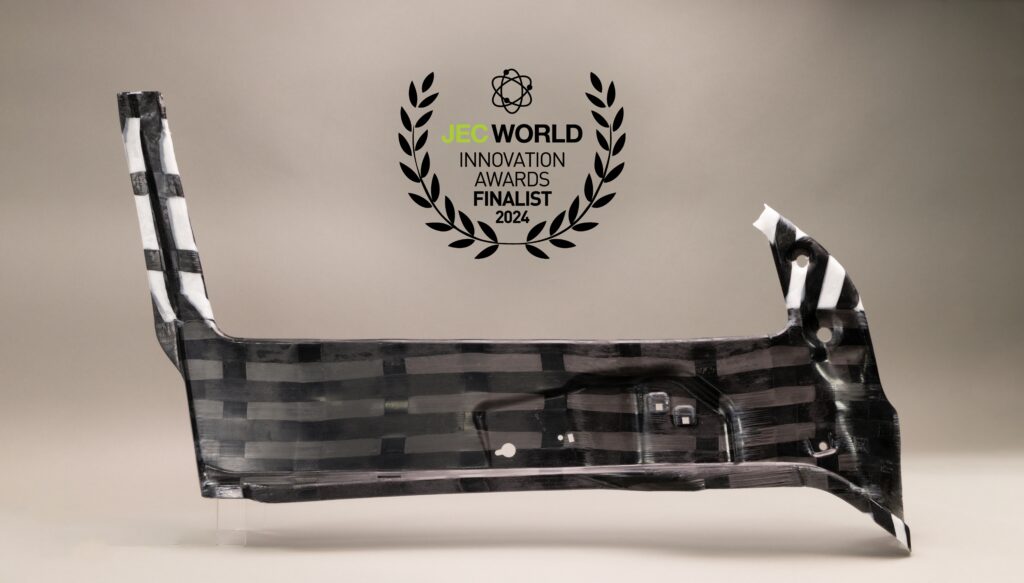
The automotive door component prototype is a beltline stiffener, made from a combination of WEAVE3D composite lattice reinforcement and Braskem polypropylene. (Photo: WEAV3D®/Business Wire)
The cost-effective demonstrator part is made from a novel combination of Braskem polypropylene and WEAV3D lattice technology.
PHILADELPHIA—Braskem and WEAV3D Inc. reported that their innovative automotive door component prototype was selected as one of three finalists in the Automotive and Road Transportation, Process category of the JEC Composites Innovation Awards 2024.
The door component prototype’s combination of WEAV3D composite lattice reinforcement with Braskem polypropylene (PP) reportedly enables lighter and less expensive thermoplastic components than conventional organo sheet. As a result, the combination is said to unlock new opportunities for the cost-effective replacement of sheet metal structures with thermoplastics throughout the vehicle.
“We continue to be very excited to offer our clients innovations and partnerships around high-performance polypropylene materials utilizing the WEAV3D lattice technology after launching this project in 2023,” said Amanda Zani, technology platform manager for Braskem, in the release. “We are honored to be recognized as a finalist for the JEC World Innovation Awards.”
Winners of the JEC Composites Awards 2024 will be announced during an online award ceremony on February 8, 2024, between 13:30 and 15:30 CET, accessible at www.jec-world.events. The Braskem-WEAV3D prototype part will also be on display in the JEC Innovation Planets section of JEC World, held in Paris, France, March 5-7, 2024.
The use of WEAV3D’s Rebar for Plastics® in combination with Braskem Polypropylene is said to offer multiple benefits versus conventional composite organo-sheet. It is said to reduce sheet blank weight by approximately 50 percent, final part weight by about 23 percent, and costs by roughly 50 percent. The technology is also reported to increase sheet yield from 25 percent to 45 percent by weight, resulting in a 62 percent reduction in trim waste.
“As the automotive industry continues to roll out new electric vehicle designs, it requires automakers to re-think the vehicle design with cutting-edge performance materials and consider more sustainable end-of-life solutions,” Zani said. “The initial conversion process focus has been on thermoforming to leverage large parts production; however, the WEAV3D technology can also be applied to injection molding of more complex parts. With significant improvements in lightweighting, reduced costs, and higher material efficiency, combining Braskem’s PP portfolio with WEAV3D composite lattices provides a ‘win-win’ in terms of enhanced material performance and a more sustainable environmental impact, including the integration of natural fiber options.”
According to WEAV3D, its patented composite forming technology integrates weaving and composite consolidation into an automated, continuous process that reduces waste, cycle times, and material handling costs. When combined with injection over-molding, thermocompression, or thermoforming, the company’s Rebar of Plastics® approach improves part stiffness and strength while minimizing weight. As a result, it is said to enable new innovations in the automotive and construction markets at a fraction of the cost and cycle time associated with traditional composite manufacturing.
“WEAV3D and Braskem are demonstrating the significant potential of the WEAV3D lattice material with this automotive door prototype, and we are thrilled to be selected a finalist by the Innovation Awards jury,” said Chris Oberste, president of WEAV3D, in the release. “Thanks to the simulation workflow developed in collaboration with Altair Engineering, we were able to optimize the lattice structure for cost and performance, while still using the original organo sheet tooling and forming process equipment at the Clemson Composites Center at Clemson University.”
Braskem, a producer of thermoplastic resins, is reported to be the largest polyolefins producer in the Americas and a pioneer producer of biopolymers on an industrial scale. WEAV3D, a startup that specializes in advanced manufacturing and materials, is described as an innovator in composite materials, manufacturing processes, and processing equipment, according to a release from the companies.