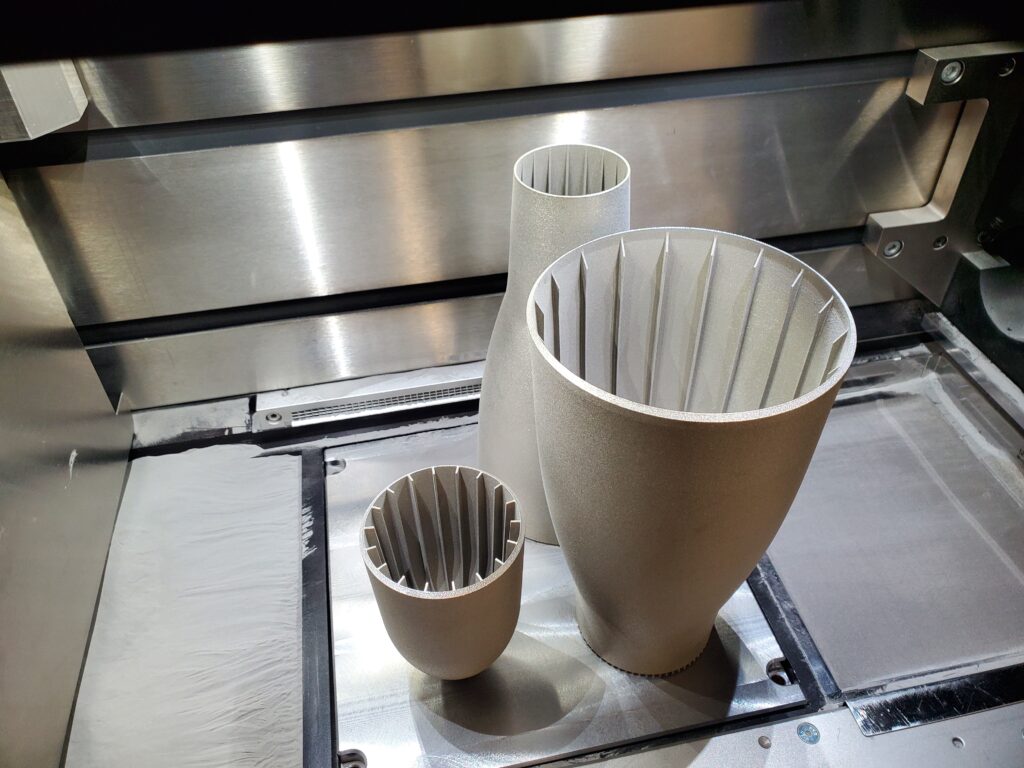
A build of multiple tall DMSL components, shown here prior to being removed from the build chamber. (Image courtesy Vetted Tech, Inc.)
At Vetted Tech Inc., U.S. veterans maximize the design advantages of additive manufacturing technology with outside-the-box thinking to produce high-performance metal and composite parts.
By Mark Shortt
A nearly four-year-old company in Syracuse, New York, is building a loyal customer base and workforce with a unique business model—excellence in rugged 3D printed parts that are manufactured solely by veterans who have served in the Unites States Armed Forces.
The company, Vetted Tech Inc. (VTI), specializes in additive manufacturing of high-performance metal and composite components for a wide range of demanding applications, from aerospace and defense to industrial. Vetted Tech uses DFARS-compliant raw materials and state-of-the-art 3D printers to produce fast-turnaround components in stainless steels, high performance alloys, and carbon fiber-reinforced composites, said Vetted Tech President and Founder Michael Mowins, in an interview with Design-2-Part.
In addition to metal and composite 3D printing, VTI provides reverse engineering services for legacy parts, as well as secondary CNC machining for post-processing of additive manufactured parts. The company is the recipient of the 2022 Onondaga County Veteran Business of the Year Award, and has won multiple HIRE Vets Medallion Awards from the U.S. Department of Labor in recognition of its efforts to recruit, employ, and retain veterans.
“We are the source for Vetted Metal™ and are a Service Disabled Veteran Owned Small Business (SDVOSB) that proudly supports the DoE, DoD, and our warfighters with a 100 percent veteran workforce,” said Mowins in an emailed response.
The company trademarked the term Vetted Metal™ to signify the steps it takes to qualify, monitor, and assure the quality of the powder materials it uses to produce high-quality parts. “We do specific quality control,” Mowins told D2P. “We control where our powder is used, we control our sources of powder, and we control the sieving and reuse of our powder to assure that the parts that we produce are of the highest consistent quality.”
Vetted Tech’s quality management system is certified to the international AS9100D (aerospace) standard for aviation, space, and defense organizations. The company is also ITAR registered, maintaining careful control over its production and export policies to ensure the items it produces are going to U.S.-friendly countries.
Vetted Tech produces medical instruments, automotive support structures, aerospace components, and armament parts, as well as various other components used in the energy, research, and industrial markets. One of its defense projects involved manufacturing a 316L stainless steel fuel sampler for the CH-47 Chinook Helicopter, as part of the AMNOW program launched by the National Center for Defense Manufacturing and Machining, according to the company’s website.
For the U.S. Department of Energy, Vetted Tech has produced numerous 316L stainless steel components with “extremely tight tolerance requirements on channels and holes,” Mowins said. The company has also worked in the medical arena, developing prototypes for non-invasive medical instruments that are critical to surgical processes.
“We don’t really get involved in the design process so much as we do in the consulting process,” said Mowins. “Most of our customers come to us with an idea and a design. And then we take that design and optimize it for additive manufacturing—in areas where we can minimize supports, optimize the performance of the part, and make it a little bit easier for us to build. That makes it lower in cost for the end user.”
Examples of VTI’s work for the automotive industry include support structures for race cars. The structures are generative designs, unlike a standard machine part that follows straight lines, Mowins said. “We’ve produced support structures out of stainless steels, as well as Inconel 625. With additive manufacturing, we can do a lot to create a very unique support structure, which minimizes the weight but also optimizes the strength of the structure,” Mowins said.
Workhorses for stainless steel parts
Unlike many 3D printing services, Vetted Tech takes time to analyze parts and optimize their build, even providing Design of Experiment pre-builds to assure conformance to tight tolerances, Mowins said. The company can print stainless steel parts up to 10 inches by 10 inches by 12 inches with its EOS M 290 DMLS machines. Mowins described the machines as powder bed systems that are “accepted worldwide as the workhorse of the additive manufacturing, direct metal laser sintering (DMLS) process.”
Vetted Tech has a dedicated line of M 290 machines that produce parts in 316L stainless steel, and another dedicated line of M 290s that print components in 17-4 stainless steel. Dedicating the machines in this manner helps Vetted Tech optimize its throughflow process by reducing changeover rates, Mowins said.
The developer of the machines, EOS, has made further iterations to the designs of their machines since introducing the M 290 models that Vetted Tech currently uses. The USM 300 and the M 400 have larger build platforms that enable the machines to print bigger parts.
“Those will probably be the next machines that we add into our stable,” Mowins said. “But our M 290s are really the global workhorse for additive manufactured powder bed parts. They literally can produce a finished part that has minimal post processing—removing some structure supports—coming straight out of the print bed.”
Exotic metal and carbon fiber-reinforced composite parts
Complementing VTI’s EOS M 290 DMLS workhorses are a suite of Markforged 3D Printers, from the latest Metal X system to the Mark Two and X7 models. The Metal X system prints metal parts via a metal fused filament fabrication (MFFF) process. It uses spools of the raw metal material—such as copper, tool steels, and Inconel 625—to produce a part layer by layer, Mowins told D2P. The part is then washed to remove binder agents, and once the binder agents have been removed, it is sintered in another machine.
“Unlike the M 290 parts that come off the print bed pretty much ready for use, the Markforged parts have to be sintered to give them the full mechanical properties in the metal that they’re being made out of. We use the DMLS process to do the 316 and 17-4 stainless steels, and the Markforged process to do the more exotic materials, like the copper and the tool steels,” Mowins said.
Vetted Tech uses its Mark Two and X7 machines to print parts in Onyx™, a chopped carbon fiber-reinforced nylon that can be reinforced with added layers of continuous carbon fiber or continuous Aramid Kevlar fiber to give the part greater strength. With a continuous carbon fiber inlay, Onyx material can provide a part with strength similar to that of a 6061 aluminum part, Mowins said.
The company uses inspection systems that Mowins called “incredibly accurate.” Its new Keyence VL and XM Systems offer 3D scanning technology that enhances VTI’s capability to perform quick and precise measurement on complex, nontraditional structures. The capability will come in handy as the company increasingly produces parts with generative designs.
“We’re looking forward to being able to measure parts that don’t have your typical straight lines and curves, which we’re seeing more and more of in our generative design parts,” Mowins said.
Vetted Tech is also using its metrology systems to help companies replace—through reverse engineering—legacy parts that can no longer be easily found. The Keyence systems provide solid models, drawings, and 3D print part files for reproduction of these parts. Vetted Tech can also use the systems to provide part-to-CAD model comparisons with tolerance heat mapping.
“Surprisingly, we thought it was going to be more of an inspection system used for parts that we build,” Mowins said. “But more and more people in our customer base and our stakeholders are coming to us and saying, ‘Hey, we’ve got this part. Can you reproduce it?’”
One customer brought over a large gear for a machine they’ve had for years. The problem was they couldn’t find replacement parts. “We’re able to take that gear, scan it, turn it into a CAD file, and actually print the part right on our machines,” Mowins said.
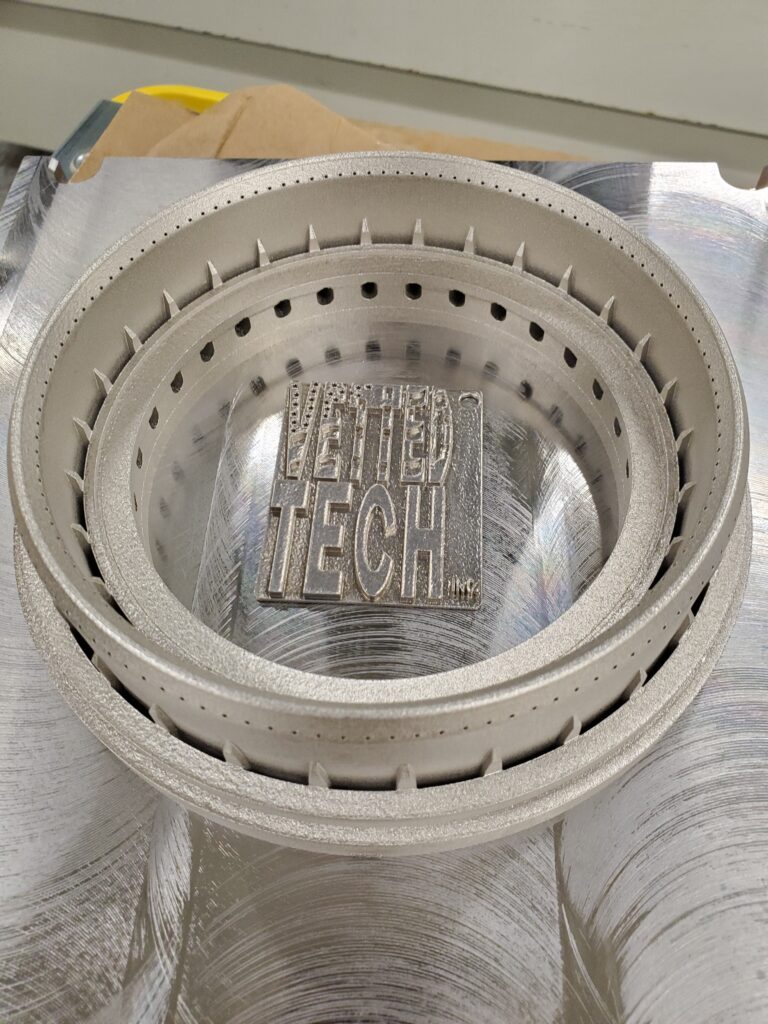
A DMLS component built in 316L stainless steel with tight tolerance holes, and assured by prior Design of Experiment. (Image courtesy Vetted Tech, Inc.)
As VTI builds its additive manufacturing capability to new levels, it continually works to optimize its throughput. Mowins said that VTI recently expanded its CNC machining capacity for the post processing of additive manufactured components.
“We look at what we can do to move parts from the print bed to delivery faster, and make sure that the quality is there,” Mowins explained. “So the addition of a 3-axis CNC machine into our operation was a real help in being able to post process some parts where we have additional support structures.”
A commitment to secure the futures of those who served
The word “Vetted” in the company’s name has two meanings, Mowins said. One is the vetting process that the company performs for its materials, processes, and the parts that it produces. The word also signifies VTI’s commitment to help veterans who are coming out of the service and looking for new employment opportunities in the civilian workforce. It’s an acronym that combines “veteran enabled transition” (VET) with “technology enabled design (TED).”
Mowins, a graduate of the United States Naval Academy, didn’t get a chance to serve in the U.S. Navy due to a physical disability he incurred while at the Academy. His experiences have led him to structure his career—and many of his volunteer activities outside of it—around giving back to veterans who had the opportunity to serve their country in the manner that he had envisioned himself doing.
“I started the company, really, as a way to give back to veterans, and so we hire and screen veterans to be employed here,” Mowins told Design-2-Part. “For me, it’s very much a commitment to our veterans, to give them an opportunity to become business owners, and to work in an industry that’s thriving and growing.”
His vision to start a business to help veterans secure their futures is supported by market research showing that additive manufacturing is indeed a thriving and growing industry. A report from ResearchAndMarkets.com projected the global additive manufacturing market to top $70 billion in 2030, on the strength of a 21.1 percent compound annual growth rate between 2022 and 2030. A similar report from Grandview Research pegged the market’s value at more than $13.8 billion in 2021, and estimated a 20.8 percent compound annual growth rate from 2022 to 2030.
“Any time you’ve got that kind of a growth trajectory for your industry, you’re going to do pretty well,” Mowins said, referring to another recent market forecast that estimated a similarly high growth rate for additive manufacturing over the next four to five years.
Vetted Tech’s website states that the company is “proud of the parts we produce, our commitment to our customers and stakeholders, and our support of those who protect our freedom.” For a company that makes parts used in the defense of the U.S., the term “stakeholders” takes on more meaning than it does for many others.
“Our stakeholders range from not only our employees and our supply chain, but also to our customers and their customers,” Mowins said. “We view our U.S. military operating forces forward as our customers as well because we produce parts that go into the defense industry, and we want to make sure that those parts function as effectively as possible for such a wide range of use and applications.”
Veterans bring nontraditional problem solving skills to manufacturing
Does Mowins see an advantage in employing veterans to make parts for the military due to the fact that they have experience in using defense equipment? Although he acknowledged that such an advantage exists, he pointed to other, more impactful strengths that veterans bring.
“The veterans who are employed here have the added advantage of knowing how a defense product might work, whether it’s munitions or arms or other items that we may produce for aviation applications,” he said. “But certainly, the other part is that the veterans have a full and meaningful understanding, more so, of mission accomplishment. We’re a small company, and we have a history of employing veterans that have dealt with mission, and dealt with the nontraditional problem solving skills that you tend to find in the battlefield or a fully deployed environment.
“We have a different approach, and we will take a look at a project and say, ‘Okay, we can do this. Let’s go find a way to do it.’ And so we thrive on the innovative process, on that nontraditional way of thinking, of being able to look at a part and say, ‘Okay, how are we going to do this?’ Knowing the capabilities of our machine and what we’re able to do with outside-the-box thinking, that you haven’t been able to do with a traditional subtractive manufacturing process, gives us that benefit.”
Vetted Tech’s Technical Director Joshua Weaver is a Syracuse University degreed civil engineer and U.S. Army veteran who embodies the nontraditional, outside-the-box approach to problem solving that Mowins described. Mowins said Weaver is “an exceptional individual who has 550 days of service in Afghanistan, in addition to the rest of his military career.”
As a combat airborne engineer with his unit in Afghanistan, Weaver designed and built a 6,000-gallon water supply that improved health conditions at his camp in Jalalabad. He also led multiple teams through complex projects, ranging from basecamp improvements to extreme engineering recovery projects. He also taught himself the foreign language being spoken around him. That skill enabled him to translate and maintain cordial relations with local citizenry that helped keep his team safe from harm, according to his LinkedIn page.
“We’re looking to add more veterans to the workforce,” Mowins said. “The real goal for Vetted Tech is to move forward as a company, grow as much as we can, develop a mindset of problem solving, stakeholder fulfillment, and really become a veteran owned organization for the veterans, to have their future secure.”