Alloy Enterprises is planning to use $26 million in recent funding to ramp up production of fully dense aluminum parts for EVs, industrial applications, and heavy equipment.
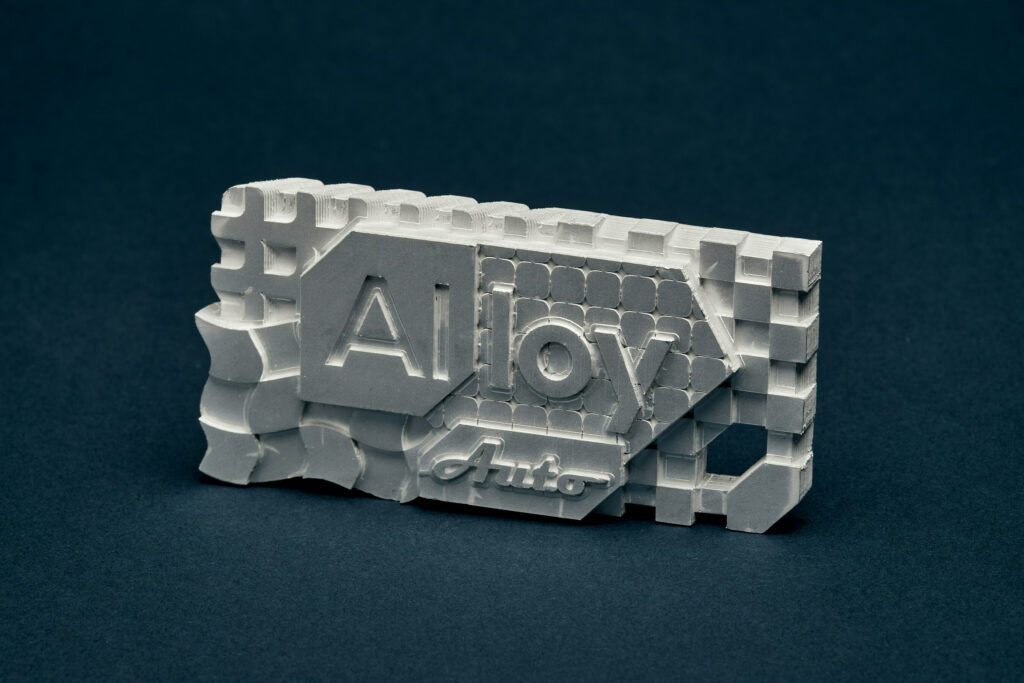
A complex aluminum part produced by Alloy Enterprises using its additive manufacturing process. The method is reported to be the first process specially designed for aluminum that does not use aluminum powder. (Photo: Alloy Enterprises via PRNewswire)
BURLINGTON, Mass—Demand for aluminum has been escalating, driven by lightweighting for e-mobility across the transportation sector and the need for more sustainable materials. But a gap exists between the demand for complex aluminum components and the supply, according to Alloy Enterprises, a Boston-area hardware startup that calls itself “the world’s first Digital Aluminum Fab.”
Alloy Enterprises said in a release that traditional manufacturing processes, such as casting, are not keeping pace with the speed of innovation. At a time when the United States has lost a large percentage of its foundries, “U.S. manufacturers need on-demand capacity, at scale, at home,” the company said.
According to Alloy Enterprises, it is filling the void with a fast, cost-effective manufacturing method that is said to streamline the production of aluminum parts at scale in the United States.
The company described its method as novel, saying it is the first process specially designed for aluminum that does not use aluminum powder. Alloy uses the process to supply complex aluminum components to its customers.
Alloy said its team uses a combination of laser cutting and diffusion bonding to produce production volumes through its machines cost-effectively. It does so while maintaining the advantages of 3D printing, such as reducing lead times, iterating designs quickly, avoiding expensive tooling, and digitizing inventory, the company said.
Venture capital firms have taken notice: Alloy recently completed a $26 million oversubscribed Series A funding round led by Piva Capital, bringing Alloy’s total raised to $37 million. The round was joined by new investors Unless, Flybridge Capital, MassMutual Catalyst Fund, and Robert Downey Jr.’s Footprint Coalition. It also includes existing investors Congruent Ventures and Riot Ventures.
“The Alloy team has proven out a highly efficient process for delivering aluminum components quickly and at scale,” said Maria Buitron, principal at Piva Capital, in the release. “This is a breakthrough for the industry that addresses the need for reasonable lead times, major cost reductions, and on-demand manufacturing, delivering direct benefits to EV, industrial, and heavy equipment. We have been so impressed with the Alloy team and look forward to partnering with them to help them scale as the need for their solution ramps up.”
Manufacturers today increasingly want the advantages of 3D printing, including complex geometries, the ability to iterate designs, and freedom from expensive tooling. But aluminum, especially alloys such as 6061, can be difficult and expensive to print using powder bed processes. The company developed its selective diffusion bonding process specifically for aluminum, with scale production in mind. Its novel feedstock is already scaled and is produced in 10-ton runs, according to the release.
Alloy Enterprises said that it plans to start delivering production volume parts this summer. The company is actively evaluating and qualifying new customer applications and said it has the capacity for volume production.
“We have an incredible team with the ability to continuously solve hard R&D challenges while staying focused on the customers’ needs,” said Ali Forsyth, CEO of Alloy Enterprises, in a statement. “We went from invention to commercial sales in less than two years. With this sizeable fundraise, we’ve added great partners to the table to help us take Alloy to the next level.”
Forsyth added that Alloy has made rapid progress, having secured Fortune 100 manufacturing customers in three major market verticals: automotive, industrial, and heavy equipment.
“We’ve proven our manufacturing process and are already qualifying customer production parts,” she said. “We will use this funding to ramp production capacity, further develop our software suite, and apply next-gen automation. We’re open for business and scaling rapidly, including hiring across the board in sales, marketing, applications, software, operations, and manufacturing.”