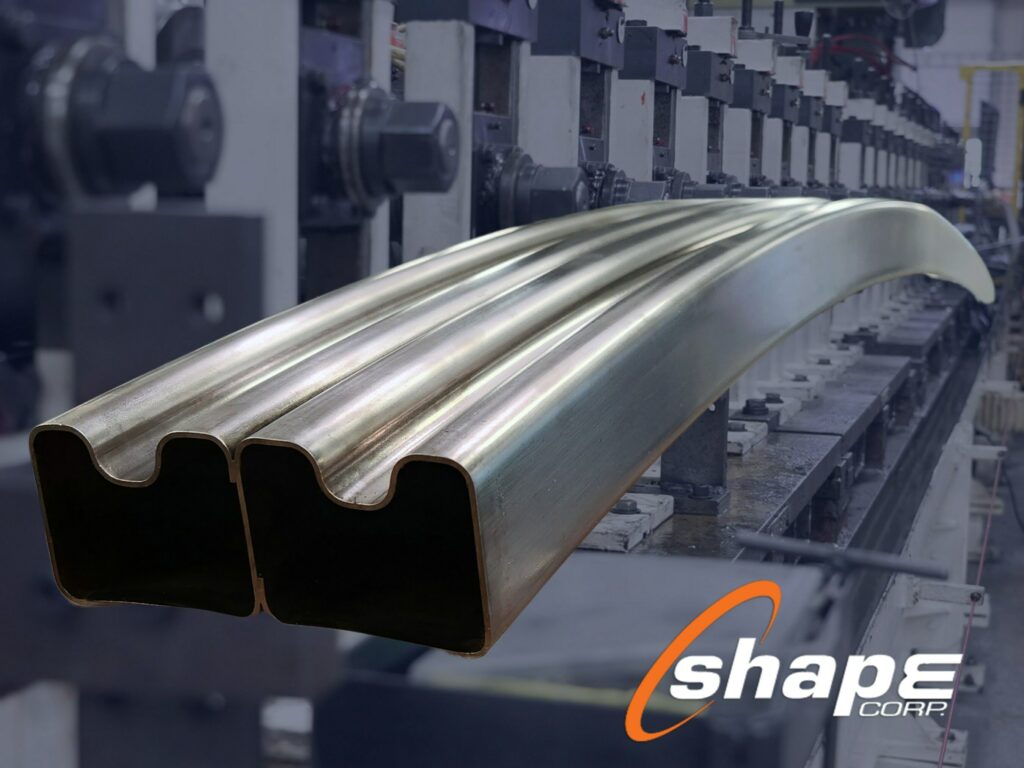
Shape Corp. announced the first roll formed production-intent martensitic steel bumper made with SSAB’s fossil-free steel material using HYBRIT technology. (Image: Shape Corp.)
GRAND HAVEN, Mich.—Tier-1 automotive supplier Shape Corp. reported the development of the first roll formed production-intent martensitic steel bumper made with SSAB’s groundbreaking fossil-free steel material using HYBRIT technology. Shape is the first automotive company to collaborate with SSAB in using the cutting-edge sustainable material in the development of this type of automotive component, the company said in a release.
According to Shape, SSAB’s fossil-free steel is based on the HYBRIT technology. The technology replaces coal with hydrogen in the reduction process, powered by fossil-free electricity. The resulting product is reported to be “virtually fossil-free.”
SSAB is planning to produce the steel at commercial scale in 2026. Shape said it has conducted rigorous testing, including bendability, fracture characterization, material toughness, delayed fracture testing, and welding evaluations that have shown the fossil-free steel does not compromise material properties or performance.
The roll forming process is reported to be considerably more sustainable than other forming processes, such as hot and cold stamping, due to the significant increase in material usage. The process not only enables usage of the highest strength materials, but also promotes efficient section design to optimize usage of the material, the company said.
The use of fossil-free steel with high material utilization and efficient use of high strength material is said to create “an exceptionally sustainable manufacturing solution.” The process, combined with the company’s committed drive towards the use of renewable energy and reducing energy consumption, is said to fortify Shape’s commitment to cultivating a circular life cycle while reducing its environmental impact.
“We are thrilled to take this significant step toward applying this steel on vehicles, marking a new era in sustainable manufacturing,” said Shape Corp. Project Manager Brian Oxley, in the release. “Our material characterization activity ensures that the performance of this fossil-free steel matches that of the incumbent steel making process.
“Considering the full scope of emissions in the steel making and part production processes, we calculate a savings of over 10.74 kg CO2 (85.7 percent) for each bumper beam produced with this steel, compared to a part made from conventional steel,” Oxley continued. “Those savings can be closer to 20 kg per part when compared to a stamped bumper of similar performance. Those savings will continue to increase as emissions from both processes are reduced further.”