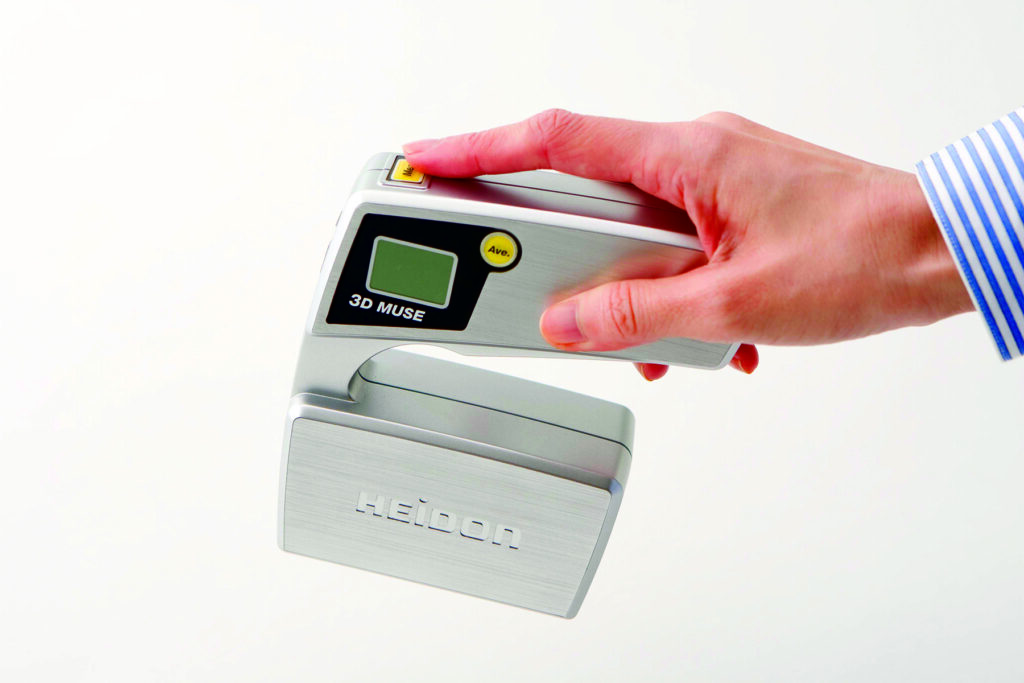
Portable, handheld instant friction testers can be used on angled or contoured surfaces to optimize the metal forming process, protect equipment, and improve product quality. (Image courtesy Kett US)
Portable, handheld instant friction testers can be used on angled or contoured surfaces to optimize the metal forming process, protect equipment, and improve product quality.
By Del Williams
Metal forming is a fabrication process in which manufacturers create a range of structural parts and components from metal sheets or tubing, bending, or deforming a piece of metal into its desired shape without any removal. The process modifies metal or a workpiece by the application of mechanical forces and often heat. Since there is contact between the forming tool and the metal being deformed, friction occurs in almost every part of the process.
Insufficient control of friction can cause excessive heat, galling, and seized parts, as well as worn edges and tools, resulting in defects. For this reason, manufacturers typically lubricate contact surfaces to facilitate the process and prevent deficiencies.
Since properly controlling friction impacts the success or failure of the metal forming process, friction testing is a vital part of monitoring and maintaining the proper conditions to produce quality products.
“In metal forming, anyone who’s had problems with lubrication, surface finish, or other friction-related issues understands that friction testers are a key piece of equipment. Unless they accurately test, they won’t know if they have a sporadic or recurring problem, which can lead to costly, out-of-spec products, until corrected,” said John Bogart, managing director of Kett US, a manufacturer of a full range of static and dynamic friction testers, as well as surface property analyzers for various industries.
The challenge is that traditional friction testing equipment is not always up to the task. Friction testing may be necessary on angled or contoured surfaces, and in multiple locations. Most traditional testing equipment, however, is not portable, requires removing a sample to the lab area, and is limited to analyzing horizontal surfaces.
As a solution, portable, handheld friction testers have been developed that enable fast, lab quality, non-destructive testing by essentially anyone without specialized training. With this capability, in situ testing of various materials and surfaces can be completed in seconds, even at an angle, upside down, or with contours.
On the production floor, this capability enables quick adjustments of lubrication and other factors to optimize metal forming, product quality, and machine longevity. In the field, it can also be used as a quality assurance (QA) check anywhere that friction testing is necessary.
Traditional Friction Testing Challenges
Traditionally, friction testing has been relegated to occasional spot checking in labs using conventional incline methods. This required destructive testing in which a portion of metal was cut from a sample, mounted on a flat plane of a second metal, with careful measurement of the inclination angle required for relative movement to start. The time-consuming process also required considerable technical expertise.
To reduce the friction during metal forming, lubricants are often used, but this can further complicate testing. Friction is frequently tested to evaluate the effect of various lubricant properties and control the results on the forming process. However, the application of lubricants essentially “changes the equation” of how much friction and force is applied in certain areas and processes of metal forming, so friction must be accurately and reliably measured to maintain consistent quality.
Another challenge in measuring friction in the forming process is the fact that many metal surfaces are not completely flat but angled, contoured, or rounded. The same is true of much of the machinery and tooling within the industry.
“In metal forming, the only material that will have a completely flat, horizontal surface is sheet metal. But once you start bending and machining, it is not a smooth, flat surface anymore, which complicates traditional friction testing,” said Bogart.
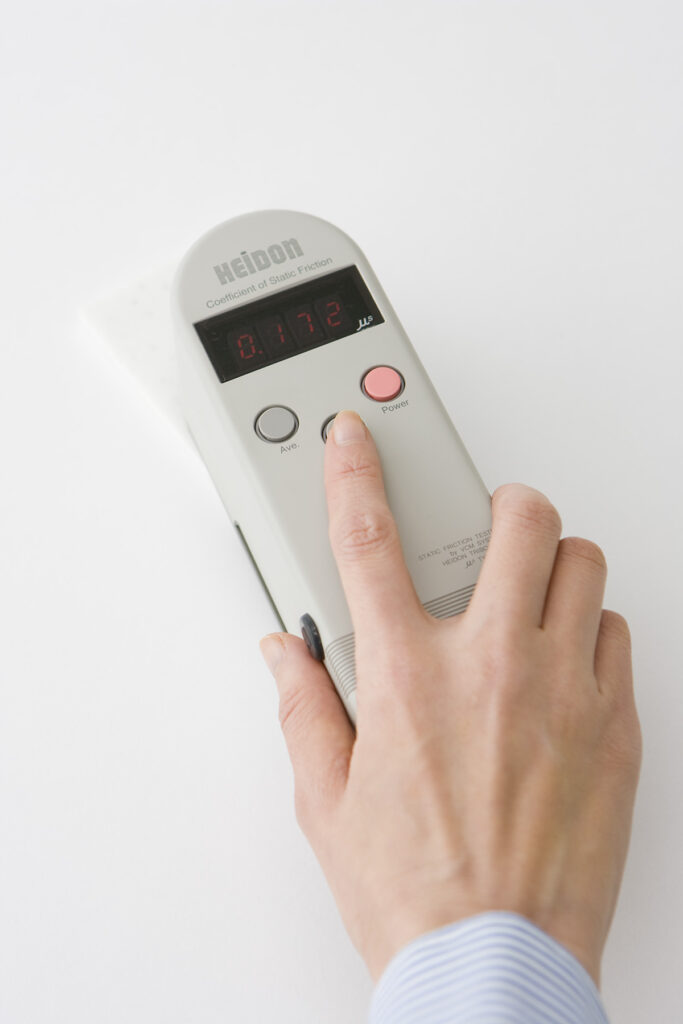
In contrast to traditional destructive incline friction testing methods performed in a lab, portable friction analyzers are now available that are simple to use. (Image courtesy Kett US)
The Benefits of Portable Friction Testing
In contrast to traditional destructive incline friction testing methods performed in a lab, portable friction analyzers are now available that are simple to use. The handheld units can be utilized anywhere virtually instant, in situ, friction testing is needed in the metal forming process. For instance, friction can be measured on metal surfaces when receiving raw materials, in production to adjust lubrication, or during QA checks further downstream.
Examples of the portable friction analyzers include two handheld, battery operated models, the H94Ai and H37 3D by Kett. Both units can measure the static coefficient of friction (SCOF) on dry, wet, or lubricated metal surfaces and are designed for use with minimal training. The operator simply places the unit on the surface to be tested, presses the “measure” key, and the static coefficient of friction is measured to 0.001 precision in seconds, with accuracy and reliability comparable to lab models.
“Basically, anyone can pull a workpiece from the production line and test the friction in multiple places with these portable units. If the item is in spec, they can put it right back on the line. If not, they can quickly adjust on the fly,” said Bogart.
For testing flexibility, the ability to exchange test fixtures allows the unit to simulate the interaction of multiple surface materials (steel-to-steel, steel-to-aluminum, aluminum-to-aluminum) by simply swapping out the fixture. This is important not only when forming various metals but also when the metal surface of the equipment and tooling differs from that of the formed material.
“Measuring friction is completely dependent on the two interface materials. So, quickly changing out the fixture to accommodate the testing of different metals is important,” said Bogart.
He noted that exchanging test fixtures can be used to simulate solid/solid interfaces and solid/liquid interfaces, which can be helpful in determining the frictional interaction of metals with lubricants or other liquids.
While the H94Ai must be held level when measuring, the newer H37 3D has integrated angle adjustments that allows it to be used at any angle—from horizontal to vertical in three dimensions, even upside down. The combination of the H37 3D’s integrated angle adjustments, along with the ability to exchange test fixtures, enables measuring friction in angled, contoured, and rounded metal surfaces. This facilitates more versatile, static coefficient of friction (SCOF) measurement of metal surfaces, machinery, and tooling, which can improve production quality and equipment longevity.
“By being able to hold the instrument at any angle, you can get accurate measurements without having to worry about either orienting the piece or orienting your hand to make sure that the instrument is completely horizontal,” said Bogart.

Portable, handheld friction testers have been developed that enable fast, lab quality, non-destructive testing by essentially anyone without specialized training. (Image courtesy Kett US)
Special fixtures can also be created for custom friction measurement applications. “By request, we manufactured a special fixture with a ‘reverse hump’ in it. The hump was the cutout [so it would sit on a bar] to simulate a friction test covering more surface than just the top of the rounded area,” said Bogart.
In addition to the portable friction analyzers, Kett offers a full line of desktop units that can be used to test not only static friction and dynamic friction, but also surface properties like peel, wear, adhesion, and scratch resistance.
Ensuring Quality, Longevity
The bottom line for the metal forming industry is that it is now easier to ensure quality and protect machinery from the problems created by either too much or too little friction in the process. With portable SCOF testing, they can ensure that all metal surfaces are within production specifications anywhere and as needed.
Del Williams is a technical writer based in Torrance, California.