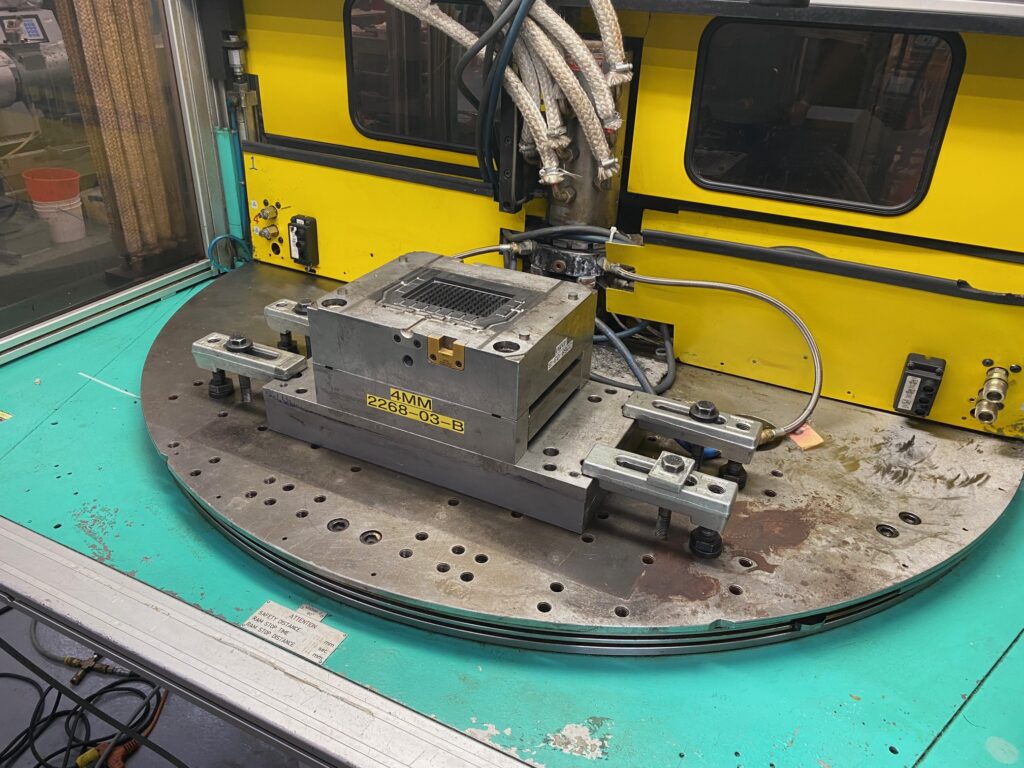
The “B” half of the mold after the finished part is removed, awaiting metal inserts. This half will rotate around to the other side, where it will join the “A” half and be filled with plastic. (Photo by Mark Langlois)
Connecticut-based PDI offers expertise in tooling design and engineered materials, along with a variety of specialized equipment.
By Mark Langlois
Plastic Design International, Inc. (PDI) offers injection molding, injection insert molding, and assembly at its two Middletown, Connecticut manufacturing plants, where the company collaborates with customers to manufacture complex parts for numerous industries.
Examples of PDI’s injection molding capabilities include diesel filtering devices for the transportation industry, electrical housings with metal inserts for the semiconductor industry, grips for the firearms industry, and fire safety pull stations for public safety applications.
The company, founded in 1977, employs about 50 people at its facilities, which total about 55,000 square feet and house 21 injection molding machines with clamping tonnage of 35 tons up to 385 tons.
“We specialize in engineering grade thermoplastics, but we offer the spectrum of injection moldable thermoplastics,” said PDI Vice President and Director of Engineering Jacek (Jake) Tuczapski, in an interview with Design-2-Part. “We are able to apply a varied degree of complexity to our tooling, depending on the part design and the customer’s requirements for any specific component.”
PDI can mold parts up to 44 cubic inches and just under 1.5 pounds in a wide range of materials. For one part, the company molded an automotive fuel filter component from glass-filled nylon, using a mold with four slides and numerous gates to ensure accuracy plus quick filling. The mold included a 3-plate ejection system.
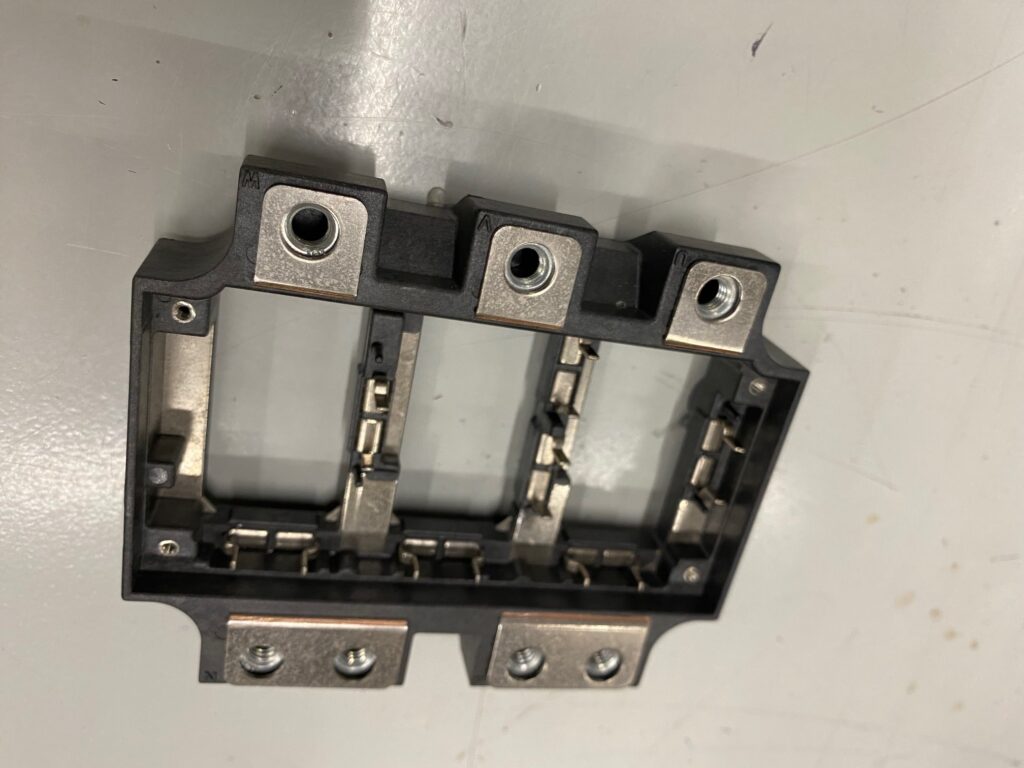
A metal insert plastic injection molded part that shows both the plastic and metal inserts. (Photo by Mark Langlois)
The part was molded using an all-electric Niigata 200-ton machine equipped with automated mold safety to ensure that all four mold-slides worked properly. One slide included an unscrewing mechanism with a hydraulically driven cylinder. The finished housing met the customer’s target goal by holding to the drawing tolerance. Now, PDI delivers economically produced parts that maintain critical requirements every week for a total of 400,000 parts a year.
The company injection molds parts from numerous plastic materials, including ABS, acetal, acrylic, copolymer polypropylene, nylon, HDPE/LDPE, polyetherimide, polycarbonate, polyester, PEEK, polypropylene, polystyrene, and polyurethane.
“Each material is engineered to satisfy specific requirements,” said Tuczapski, adding that fillers, reinforcements, and additives are used to achieve dimensional and end-use component and application requirements. The part won’t shrink as much with glass in it, making it easier to hold the size. A particular part may have 30 measurable dimensions, but only a handful are critical. PDI learns the customer’s goals and what is essential through close communications.
“You want a tighter tolerance, you pick the material with the least shrinkage,” Tuczapski said during a plant tour. “Glass doesn’t shrink—plastic shrinks.”
Pump Housing for Diesel
An example of a complicated part created in cooperation with the customer is a pump housing for a power hydraulic filter. PDI recommended a carbon and glass reinforced, heat-stabilized polyamide 6/6. It had the strength, dimensional stability, and resistance for the heat and abrasion it sustains while in use. The mold had two unscrewing cores.
The PDI team used its all-electric 310-ton injection molding press with advanced control features, giving it the ability to hold an extremely tight tolerance. Its engineers worked with the customer through product development and design, through the material selection, mold design, insert molding, and secondary operations, to meet the customer’s goals. Now, PDI is making roughly 10,000 pieces a year.
In-House Mold Maintenance and Repair
Plastic Design International began as a short-run prototyping R&D shop making molds for customers, and it has evolved into injection molding in small, medium, and long runs. One of its specialties is insert injection molding. The company maintains its machine shop for mold fabrication, mold maintenance, engineering changes to molds, and for mold repairs.
Tuczapski explained that keeping the machine shop in-house at PDI is critical for lowering the cost to customers and for running an economical injection mold business. Once the customer and PDI have a mold and after it passes inspection and early runs, the customer frequently decides days, weeks, or months later that the mold must be modified. Those changes are a normal step in a part’s evolution. Maybe the part must be larger, or the part must be smaller, but the mold must change. By performing those changes at PDI, the work is done faster without relying on an outside vendor.
He estimated that customers might change a mold, after it is approved and tested, about half the time. If a customer has an issue, they may want to increase the geometry, change a hole size, change a rib size, or change an angle.
“That’s an engineering change,” Tuczapski said. “We do all the engineering changes here. Other companies don’t have the people we do.”
The company, ISO certified since 1996, maintains an ISO 9001:2015 certification for “custom injection molded components and value-added services for original and aftermarket equipment manufacturers,” according to its certificate of registration. PDI also maintains an active CAGE Code and is ITAR compliant.
A Big Step Forward
Tuczapski has worked for more than 20 years with PDI. He said the company took a big step forward nearly two decades ago when it added vertical insert molding presses, which make it easier and less costly to perform injection insert molding. The metal inserts may have threads for enclosures or flat metal terminals for electronic connections, among other insert purposes. In some instances, the metal inserts are put into a mold first, and then the mold closes and the liquid plastic is injected. In other cases, the inserts can be sonic welded or inserted later.
In another part example, PDI worked with a customer in the fire protection industry to create a tight-tolerance, plastic injection molded assembly by integrating several assemblies in the molding process. The material was a polystyrene-based conductive thermoplastic compound requiring tight temperature control, and two molds were built to produce in excess of 10 million parts.
To maintain the required conductivity level, PDI blended in steel fiber in “Mold 1,” which molded an inner chamber. The mold featured four cavities with a hot manifold and 12 cams for rapid cycle times. The second mold (Mold 2) had eight cavities and two hot-drop manifolds that allowed for closed loop recycling of the runners. Additional finishing operations included welding the air deflector and bug screen to the inner chamber.
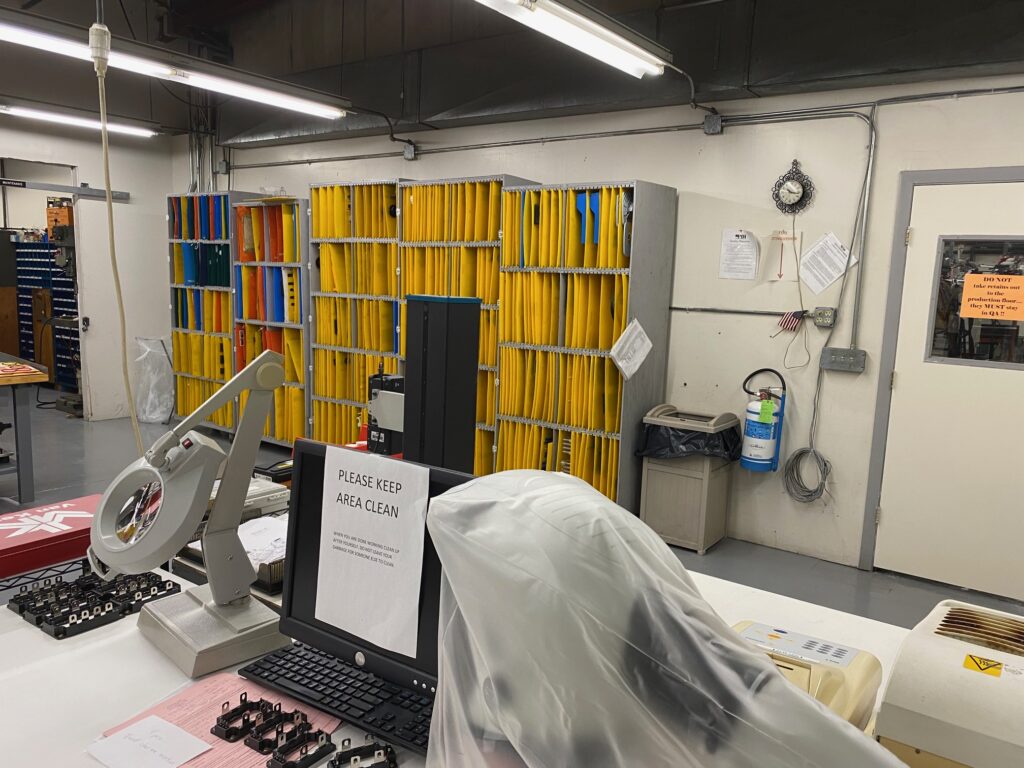
The far wall is covered in shelves that hold criteria boards so workers can compare a finished piece to what PDI and the customer require for an approved finished piece. (Photo by Mark Langlois)
Insert Molding a Medical Part
For one medical laboratory, PDI molds a part using a rotary table, x2B ½ mold in a two-step process. After removing a finished part, the machine technician sets 24 aluminum inserts in the now empty mold “B” half nearest the machine technician. At that moment, on the far side of the table, the other “B” half fits with the “A” half. It is then injected with plastic. The machine rotates, and the machine technician removes the finished part and sets the 24 inserts. On the other side, the A and B sides come together and the machine injects the plastic. The machine rotates.
The machine technician then removes the finished part and sets another 24 inserts in the now empty nearby B side. That cycle continues.
“Everybody is used to molding two or three inserts. This is 24 and they have to be dead on,” Tuczapski said. “While one is being loaded with the inserts, the other side is being plastic injection molded. Basically, you’re gaining output. It’s twice as fast.”
PDI’s 150-ton and 200-ton vertical platen molding machines are designed to support a range of insert molded components.
Molding Electronics into the Center
Another specialty of PDI is the ability to put electronics or metal at exactly the center of a plastic injection mold. In one case, working closely with the customer’s engineers, PDI designed a process using an aromatic polyester-based thermoplastic that allowed PDI to mold a nearly 14-inch plastic antenna around the electronics with a wall thickness of only 0.055 inch. The antenna is used for portable radio communications.
“That is proprietary,” Tuczapski said. “A lot of people try this and fail. We have this capability of overmolding an antenna and keeping the steel rod in the center.”
The company is adding collaborative robots to its operations. It is setting up a Universal Robots UR 10 to machine tend a medical part. The robotic arm will take the finished parts and box them. The part itself is a component used to manage radioactive waste. One goal of using cobots is to improve PDI’s competitive standing in the industry by lowering labor costs.

A metal criteria board that shows errors or problems that must be fixed before a part can be approved. (Photo by Mark Langlois)
“We invested in a collaborative robot. Our process engineer just went to Boston for the training. We hired this guy,” Tuczapski said, patting the robot on the elbow. “By the end of the year, we plan to hire more of them. They don’t get Covid, they don’t get bored, they don’t get tired. We want to hire that kind of operator so that our machine operators can have the time and focus to develop new skills and add higher value while reducing repetitious tasks.”
This shift toward cobots is just starting at PDI. The company is learning what the cobots can do and learning how to program them and wire them.
On the factor level and in addition to ISO procedures and processes, the company applies a standardized visual management system with physical sample retains for all components manufactured.
“That isn’t left up to chance,” Tuczapski said. In addition to being measured, all parts are subject to controlled, predetermined, and agreed upon standards. The company uses a moisture analyzer to measure their moisture content prior to each start-up. “We follow the directions from the material manufacturer,” he said.
What Is Plastic Injection Molding?
Plastic injection molding is a manufacturing technique that involves melting a polymer into liquid, and then forcing it under high pressure into a mold. Once the molten plastic cools, the now solid part is removed from the mold, and the process repeats, making plastic injection molding a reliable and cost-effective manufacturing method, Plastic Design International (PDI) said on its website.
The success of the manufacturing process hinges in part on the skills required to carefully design and build the mold, so that the part inside can be properly molded time after time. Each corner, cavity, and crevice of the mold design is filled. As the parts are molded, PDI monitors and checks the mold to ensure each part is manufactured properly.
Plastic Design International listed lower scrap rates, higher part complexity, and greater cost-effectiveness as three advantages of injection molding. The process produces less scrap than machining, a subtractive method that removes excess material from a larger initial piece to form a part. Injection molding generates less waste because only the precise amount of material needed to fill the mold cavities is used. In thermoplastic injection molding, the gates (feeder lines) and flash (thin wing-like waste sometimes left between mold halves) can be recycled.
Injection molding can be used to create complex parts that require complex molds. These molds can accommodate a wide range of parts and wide range of intricate part designs. Complex and intricate designs are possible because the high pressure applied to the molten polymer ensures that each section of the mold is fully filled.
Injection molding is cost-effective because while the initial design and mold construction is costly, once completed, the molds can be used and reused many thousands of times. Plastic Design International has an entire mold maintenance department devoted to keeping molds in top condition to continue precise and continuous production. The production process can also be automated, which lowers costs for time and labor while reducing the chances of defects.
How does injection molding compare to other processes?
Injection molding is similar to blow molding with several key distinctions. Injection molding creates a solid plastic piece. Blow molding creates a hollow plastic piece. In the design process, customers must decide whether they want a solid component or a hollow component.
When comparing injection molding to 3D printing, a couple of questions must be answered. Injection molding typically takes longer, often requiring about five to seven weeks for simple designs. More complex tool designs require more time and money. The process makes financial sense if roughly 1,000 parts or more are required. Depending on the material and the part requirements, some post processing work may be required, including assembly, hot stamping, machining, sonic welding, flushing/cleaning, hardness testing, moisture testing, and others.
3D printing can produce parts more quickly, sometimes in less than two weeks. It also works well if frequent design changes are required. It typically works for small pieces in small quantities, but secondary processes may follow the initial build, including washing and sometimes curing. Other secondary processes may include sanding, coating, plating, or media blasting.